aluminum

Figure 1. The main extraction process for aluminum makes use of electrolysis. Alumina (aluminum oxide), obtained from bauxite, is dissolved in molten cryolite and direct-current electricity is passed between carbon electrodes. Aluminum 99.8% pure sinks to the bottom and can be purified further if need be.

Figure 2. Aluminum.

Figure 3. Bauxite. Credit: Mineral Information Institute.
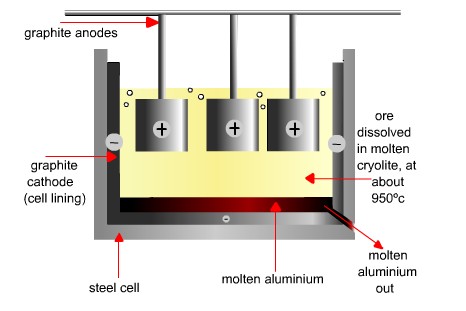
Figure 4. The electrolysis of aluminum ore dissolved in molten cryolite.

Figure 5. Aluminum and its alloys have a myriad of uses, from spacecraft to cooking foil. Many different elements may be added to aluminum .

Figure 6. The increasing hardness of aluminum .

Figure 7. A thin film of oxide rapidly forms on aluminum on its exposure to air. Unlike rust on iron the oxide film is hard and non-porous, making aluminum non-corrodible but difficult to weld.

Figure 8. Anodizing [A] is the name of the electrolytic process for deliberately forming a relatively thick film of oxide on aluminum and its alloys. The article to be anodized (3) is made the anode (positive anode) in an electrolyte (1), or generally chromic or sulfuric acid. The circuit is completed through an inert cathode [2]. The thin atmospheric oxide layer [B] is broken down so that further oxidation, to form a thicker layer [C], can take place. Anodized aluminum can be dyed various colors, including metallic ones to make it resemble, say, brass or copper. The oxide layer is then sealed [D]. Letters and symbols can be made photographically. The process is more than merely decorative finish and gives a tough surface that is much harder than the original base metal..

Figure 9. The electrical conductivity of aluminum (Al) is only about 60% that of copper (Cu) but Al is lighter and cheaper. Here [A] weights and resistances are compared for 1,000 meters of cable – Cu [B] and Al [C].

Figure 10. Polished aluminum reflects much more light than iron and nearly as much as silver, making it an ideal material for telescopes and other optical instruments.

Figure 11. Thirty-nine duralumin rings attached to lateral girders formed the lightweight but strong 803-foot-long framework of the Hindenburg.
Aluminum (Al) (British: "aluminium") is a lightweight, silvery-white, ductile, malleable, metallic element in group 13 (old group IIIA) of the periodic table (Figure 2). Its name comes from alumen, the Latin name for the mineral alum.
![]() |
Arrangement of atoms in the aluminum crystal lattice
|
Aluminum is soft because its atoms form a close-packed, cubic structure. This has many glide planes to let the atoms easily slide over each other. It is malleable and easily drawn out into the wires.
At the beginning of the 19th century Humphry Davy had postulated the metals' existence but was unable to isolate it from its compounds in a sufficiently pure state to learn anything about it. In 1825 it was first isolated in a reasonably pure form by by Hans Christian Oersted but it was not until 1845 that Friedrich Wöhler succeeded in producing a sufficient quantity to discover that aluminum was both very light and malleable.
atomic number | 13 |
relative atomic mass | 26.98154 |
electron configuration | 1s22s22p63s23p1 |
atomic radius | 143.1 pm |
oxidation state | 3 |
melting point | 660.3°C (1,220.6°F) |
boiling point | 2,519°C (4,566°F) |
relative density | 2.69 |
Occurrence
Aluminum is the most abundant element in Earth's crust (8%), but, being chemically reactive, is only ever found in combination with other elements. Its chief ore is bauxite but it is also found in cryolite, feldspar, clay, and many other minerals.
Bauxite
Bauxite is the main ore of aluminum – the source of over 99% of the metal (Figure 3). It is the name for a mixture of similar minerals that contain hydrated aluminum oxides; usually iron oxide is present as an impurity. These minerals are gibbsite (Al(OH)3), diaspore (AlO(OH)), and boehmite (AlO(OH)). Because it is a mixture of minerals, bauxite itself is a rock, not a mineral. It is reddish-brown, white, tan, and tan-yellow. It is dull to earthy in luster and can look like clay or soil. Bauxite forms when silica in aluminum-bearing rocks (that is, rocks with a high content of the mineral feldspar) is washed away.
High-grade bauxite, being highly refractory, is used as a lining for furnaces. Synthetic corundum is made from it, and it is an ingredient in some quick-setting cements.
Australia has huge reserves of bauxite, and produces over 40% of the world's ore. Brazil, Guinea, and Jamaica are important producers, with lesser production from about 20 other countries.
Cryolite
Cryolite is a brittle, icy-looking red, brown, or black halide mineral, sodium-aluminum fluoride (Na3AlF6) found in pegmatite dikes (Greenland has the only large deposits). It occurs as crystals in the monoclinic system, occasionally the cubic system, sometimes as granular masses. The crystals are frequently twinned. Molten cryolite is used to dissolve bauxite ore in the electrolytic production of aluminum. Cryolite is also a source of aluminum salts and fluorides.
Extraction
When, in the mid-19th century, it was realized that aluminum is so lightweight, Napoleon III (1808–1873) saw its potential for military use and provided money for the French chemist Henri Saint-Claire Deville (1818–1881) to develop a process for its large-scale production. Deville devised a process based on the chemical reduction of aluminum chloride using sodium metal and aluminum was displayed publicly at the Paris Exhibition of 1855. At this time it cost about $250 per kilogram, but by 1886 the price had dropped by $15 per kilogram and a total of 50 tonnes had been produced.
Hall-Héroult process
The future of aluminum was assured in 1886 when at almost the same time, Charles Martin Hall (1863–1914) in the United States and Paul Louis Toussaint Hèroult (1863–1914) in France devised the process for extracting aluminum by electrolysis that is still used today. In the Hall-Héroult process (also known simply as the Hall process), pure aluminum oxide, extracted from bauxite, is dissolved in molten cryolite at 970°C, and subject to electrolysis with a current of about 100 kA, through carbon electrodes. Molten aluminum is formed at the cathode and withdrawn from the bottom of the cell (Figures 1 and 4).
Uses
Aluminum is extremely useful for several reasons (Figure 5). First, it is light – weighing only about a third as much as other common metals for the same volume. It is also strong, and to give the same rigidity need weigh only half as much as steel. Its strength can be greatly increased by alloying with other metals (Figure 6).
Second, although aluminum combines readily with other elements, including oxygen, it does not rust or corrode in the air, because a thin film of oxide is formed on the surface, and this protects the metal below (Figure 7). So aluminum has excellent corrosion resistance.
Third, aluminum conducts heat and electricity extremely well (Figure 9). An aluminum wire will conduct only 60% as much electricity as a copper wire of the same size, but more than twice as much as a copper wire of the same weight. Its good heat conducting qualities and its resistance to corrosion have led to its widespread use in cooking vessels.
Aluminum is widely used for aircraft parts, engines, window frames, pans, drinks cans, kegs, cooking foil, etc., and to form many hard, light, corrosion-resistant alloys.
Aluminizing
Aluminizing is the process of coating a mirror with aluminum. The aluminum is vaporized in a vacuum, causing a film of metal, about 100 nanometers thick, to be deposited on the glass. Layers of other materials, such as silicon dioxide, may subsequently be laid down to give protection. Aluminum offers consistently high reflectance throughout the visible, near-infrared, and near-ultraviolet regions of the spectrum.
Before the 1930s, when the vacuum aluminizing technique was developed, the only method available for coating mirrors was silvering in which the silver was deposited chemically by a process developed by the German chemist Justus von Liebig. The initial reflectivity of silver (89 to 93%) is slightly higher than that of aluminum throughout most of the visible spectrum, but this advantage is short-lived because silver quickly tarnishes, whereas the reflectivity of an aluminum coating drops by only a few percent per year. Silver, too, is much more expensive. See also speculum.
Duralumin
One of the most important alloys of aluminum is duralumin, an alloy containing about 4% copper with smaller quantities of magnesium (1%), manganese (0.7%), and silicon (0.5%). It was invented in 1908 by a German engineer, Alfred Wilm. This alloy has been very important in the development of aviation, beginning with its use for Zeppelins in World War I, owing to its combination of strength and lightness (Figure 11). It is not as resistant to corrosion as pure aluminum, but when high corrosion resistance is needed it can be coated on both sides with a layer of pure aluminum.
Compounds of aluminum
Compounds of aluminum are trivalent and mainly cationic, though with strong bases aluminates are formed (see also alum).
alumina oxide (Al2O3), or alumina, is a colorless or white solid occurring in several crystalline forms. The impure hydrated form of alumina, bauxite, is the chief ore of aluminum. Other forms of alumina include corundum, two impure varieties of which are the gemstones ruby and sapphire. Solubility in acid and alkali increases with hydration. Melting point 2,045°C, boiling point 2,980°C. Alumina is used as an abrasive, an electrical insulator, and a furnace lining.
aluminum chloride (AlCl3) is a colorless crystalline solid, used as a catalyst (see Friedel-Crafts reaction). The hexahydrate is used in deodorants and as an astringent.